Introduction: Understanding Three-Phase Motor Connections
Three-phase motors are the backbone of industrial applications, powering everything from large factory machines to HVAC systems. However, proper motor connection and wiring are often overlooked, even though they are crucial for the motor’s efficiency, longevity, and safety. Whether you are an experienced electrician or just starting, understanding the general manual and connections for three-phase motors is essential.
In this article, we’ll dive deep into the different types of three-phase motors, explore their wiring configurations, and provide a step-by-step guide for proper installation. We’ll also cover troubleshooting common issues that can arise with connections, and answer frequently asked questions related to motor wiring.
Let’s get started with the basics.
What is a Three-Phase Motor?
1.1 What is a Three-Phase Motor?
A three-phase motor is a type of electric motor that uses three separate alternating currents (AC) to produce motion. Unlike single-phase motors, which rely on just one AC power source, three-phase motors use three phases that are 120 degrees apart. This setup provides a continuous and stable power supply, making these motors ideal for high-performance applications.
The primary difference between a single-phase motor and a three-phase motor lies in the way electricity is delivered. A three-phase system delivers power in a more constant flow, resulting in smoother operation, less vibration, and greater efficiency. These motors are typically used in industrial settings, where high power and constant, reliable performance are essential.
1.2 Why Understanding Connections is Crucial
When wiring a three-phase motor, proper connections are paramount. Incorrect wiring can lead to motor malfunction, overheating, or even complete failure. Furthermore, without understanding the correct wiring configuration, it’s impossible to fully tap into the motor’s potential power.
For example, wiring a three-phase motor incorrectly can cause it to run inefficiently, or even reverse the rotation direction, which may not be desirable for many applications. This is why it’s crucial to follow the manual provided by the motor manufacturer and understand the various types of wiring configurations—star (wye) and delta—each serving a different purpose based on the voltage and current needs of the system.
The right wiring ensures optimal performance, saves energy, and prolongs the lifespan of your motor. By the end of this article, you’ll be equipped with the knowledge to handle these connections confidently. So, let’s move on to the different types of motors and how to connect them properly.
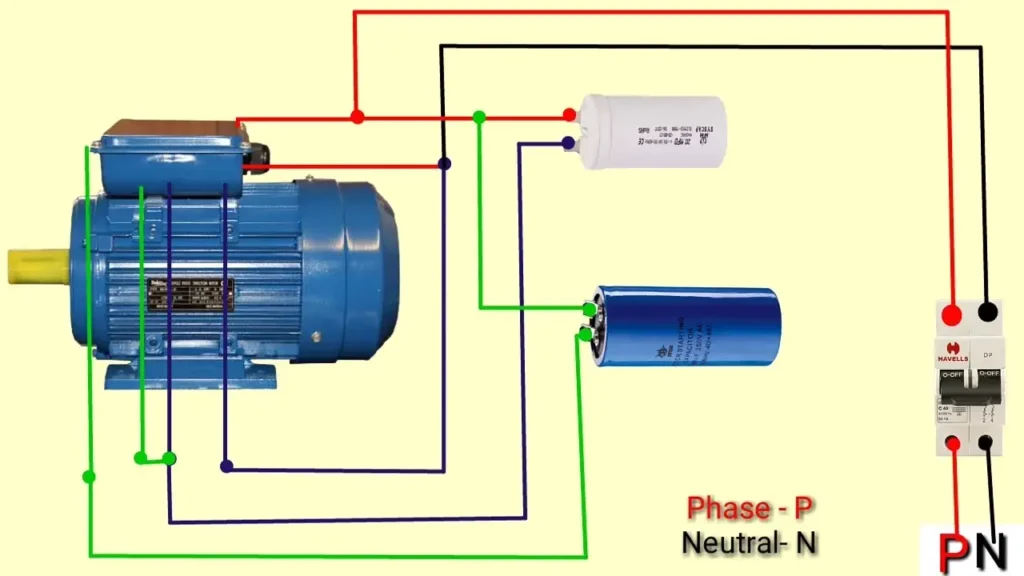
Types of Three-Phase Motors
Squirrel Cage Induction Motor
The squirrel cage induction motor is by far the most commonly used type of three-phase motor in both residential and industrial applications. Its name comes from its rotor design, which resembles a squirrel cage—a simple but efficient structure. This type of motor operates on the principle of electromagnetic induction, where the rotating magnetic field induces a current in the rotor. The rotor then creates its own magnetic field that interacts with the stator’s field to generate motion.
What makes squirrel cage induction motors popular is their durability and low maintenance requirements. Since they have no brushes or commutators, there’s less wear and tear, which makes them ideal for continuous operations. These motors are typically used in pumps, fans, compressors, and many other systems where reliable, high-efficiency performance is needed.
Wound Rotor Induction Motor
While less common, the wound rotor induction motor (WRIM) has applications in situations where high starting torque or adjustable speeds are required. Unlike the squirrel cage motor, the rotor of a WRIM consists of coils (wound copper windings) that are connected to external resistors, making it a more complex design. The external resistors help in controlling the motor’s starting characteristics, allowing for smoother startup and better control under load.
Wound rotor motors are often used in heavy-duty applications, such as large conveyors and mills, where high torque is needed during startup. However, they are more expensive to maintain due to their brushes and the need for regular servicing.
Synchronous Motors
A synchronous motor is another type of three-phase motor, but it operates differently from both squirrel cage and wound rotor motors. In a synchronous motor, the rotor rotates at the same speed as the magnetic field produced by the stator, meaning it runs at a constant speed regardless of load. This makes it ideal for precision applications requiring stable speed, such as in synchronous clocks or in industrial equipment where exact timing is crucial.
Synchronous motors are often used in power factor correction, as they can be engineered to provide a leading power factor, helping to balance the overall power quality in an industrial setting. However, they typically require an external source of excitation (like a DC supply) to create the rotor’s magnetic field, which adds complexity.
Each type of motor serves a specific purpose depending on the operational needs of the system. Whether you need a simple, rugged solution like the squirrel cage motor, or a more complex, high-torque option like the wound rotor, understanding the distinctions will help in choosing the right motor for your application.
Understanding Motor Phases
What Are Motor Phases?
In a three-phase motor, the term “phases” refers to the three alternating currents (AC) that flow in the system. These currents are separated by 120 degrees in time, meaning each phase reaches its peak voltage at a different time. This setup creates a balanced and consistent power flow, which allows the motor to run smoothly. Each phase contributes to the overall operation, and together, they generate the rotating magnetic field that drives the motor’s rotor.
Unlike single-phase motors, which can experience power fluctuations or dips in current (leading to vibrations and inefficient operation), three-phase motors provide continuous power. This continuous flow eliminates the need for a power storage system and ensures the motor operates with a much higher level of efficiency.
The key feature of a three-phase motor is its ability to produce a constant torque, unlike single-phase motors that only generate torque at certain points during the cycle. This leads to smoother startup and operation, as there are no interruptions in power.
How Phases Affect Motor Performance
The performance of a three-phase motor is highly dependent on the balance of the phases. Ideally, the current in each phase should be equal, ensuring that the motor runs smoothly and without strain. If the phases are imbalanced, the motor may experience issues such as overheating, reduced efficiency, or even failure in extreme cases.
For example, when the phases are unbalanced, one phase may carry more current than the others, leading to excessive heat generation in the motor windings. This can cause the insulation to break down and potentially lead to a complete motor failure. This is why regular maintenance, which includes checking for phase imbalance, is crucial for the longevity and proper functioning of a three-phase motor.
Another factor that influences performance is the voltage level provided to each phase. If the motor is receiving different voltages in each phase, it may cause the motor to run inefficiently, or worse, damage the motor. Therefore, ensuring that each phase receives the proper voltage is key to maintaining optimal motor performance.
Phase Sequence
In addition to maintaining a balanced load, the phase sequence also plays a vital role in ensuring the proper functioning of the motor. The phase sequence determines the direction in which the motor’s rotor will rotate. This is crucial in applications where direction matters, such as conveyor belts or industrial fans.
If the sequence is incorrect, the motor will rotate in the opposite direction, which could lead to operational failures or equipment damage. To ensure the correct phase sequence, many systems incorporate phase rotation meters that verify the proper phase order before the motor is connected.
If the phase sequence is reversed, you can fix it by swapping any two of the three incoming power lines. This action will correct the direction of rotation and restore proper operation.

Wiring Configurations for Three-Phase Motors
Star (Wye) Configuration
The star (or wye) configuration is one of the most common ways to connect a three-phase motor. In this setup, one end of each of the three windings is connected together at a central point, forming a “star” shape. The other ends of the windings are then connected to the three-phase power supply. This central point is known as the “neutral,” and it serves as a return path for the current.
One of the main advantages of the star configuration is its ability to reduce the voltage that each winding experiences, which can help minimize current draw during startup and make the motor more energy-efficient. This is particularly beneficial for high-voltage systems, where reducing the voltage across the windings can prevent overheating and improve longevity.
The star configuration is most commonly used in motors that are designed to operate at lower torque levels or that need to run at reduced speed during the initial startup. It’s often used in applications where the motor will eventually run under full load after the startup phase, and in motors designed for dual-voltage systems (like motors rated for 230/460 V).
Delta Configuration
In contrast to the star configuration, the delta connection provides a higher starting torque and operates the motor at a higher voltage. In this configuration, the ends of each winding are connected to the beginning of the next, forming a triangular “delta” shape. Each of the three windings is connected to one phase of the power supply.
The delta connection is typically used in applications where the motor needs to operate at full capacity from the start. It’s ideal for high-torque applications such as compressors, pumps, or large conveyor systems. While it offers better performance in terms of torque, the delta configuration also results in higher current draw, which can lead to more heat generation and increased energy consumption.
For motors with a dual-voltage capability, the star-delta switch can be used to initially start the motor in star configuration (for reduced voltage) and then switch to delta for full voltage operation once the motor reaches its operating speed. This method helps in managing the startup current and ensures a smoother operation without stressing the motor’s electrical system.
Dual-Voltage Configurations
Many three-phase motors are designed to operate with dual voltage options, such as 230 V and 460 V. The dual-voltage configuration allows the motor to be rewired to suit either a low-voltage (star) or high-voltage (delta) system, depending on the available power supply.
For example, if a motor is rated for 230/460 V, it can be wired in star for use on a 230 V supply, or in delta for use on a 460 V supply. The main advantage of dual-voltage configurations is the ability to use the motor in different environments and applications, which helps make the motor more versatile.
In dual-voltage motors, the internal winding connections need to be changed to switch between star and delta configurations, so it’s essential to follow the manufacturer’s wiring diagram carefully to avoid damage or improper operation.
Steps for Properly Connecting a Three-Phase Motor
Gathering the Necessary Tools
Before starting the wiring process, it’s important to gather all the necessary tools. Here’s a quick checklist of what you’ll need:
- Wire strippers: To strip the insulation off the wires without damaging the copper conductors.
- Screwdrivers: For tightening connections on terminal blocks and the motor junction box.
- Circuit tester: To check if the power supply is correctly wired and to ensure there are no live wires during installation.
- Wrenches: To secure grounding connections and ensure proper installation.
- Cable cutters: To cut wires to the correct length.
- Phase rotation meter: To verify the correct phase sequence, ensuring the motor rotates in the right direction.
Ensure that you have these tools on hand and that they are in good working condition before beginning the installation.
Motor Preparation
Once the tools are ready, it’s time to prepare the motor. Before connecting it to the power supply, make sure to inspect the motor thoroughly:
- Check the motor nameplate: The nameplate will contain important information such as voltage, current, and phase specifications. Ensure that the motor matches the power supply in terms of voltage and phase.
- Inspect the motor windings: Look for any signs of damage, corrosion, or wear. If you notice any issues, it’s best to address them before proceeding with the installation.
- Verify motor shaft alignment: The shaft should be aligned properly to prevent any misalignment when the motor is running. This will help avoid unnecessary vibrations or wear and tear on the bearings.
- Ensure proper grounding: Safety is paramount when working with electrical systems. Be sure to check that the motor is grounded correctly to avoid electric shocks or fires.
Once you’ve confirmed that the motor is ready, it’s time to connect it to the power supply.
Connection to Power Supply
Now that the motor is prepared, you can begin the actual wiring process. Here’s a step-by-step guide to connecting a three-phase motor to a power supply:
- Turn off the power: Before making any connections, ensure that the power supply is turned off. Use a circuit tester to verify that the lines are not live.
- Access the motor terminal box: Most three-phase motors will have a terminal box where the wiring connections are made. Open the terminal box carefully, and you’ll usually see three terminals labeled U, V, and W for each phase connection.
- Identify the power supply leads: The three-phase power supply will have three leads—one for each phase. These should be color-coded (commonly red, black, and blue), but be sure to double-check the wiring diagram for your specific motor.
- Connect the phases to the motor: Using the wiring diagram provided by the manufacturer, connect the power supply leads to the motor terminals (U, V, and W). If you are using a star configuration, connect the neutral point (often marked as “N”) to the center of the motor windings.
- Secure the connections: Tighten the screws to secure the wires in place. Make sure there is no risk of loose connections, as this can lead to overheating or equipment damage. Use a torque wrench if necessary to ensure the correct tightness.
- Check the phase sequence: Use a phase rotation meter to ensure that the phase sequence is correct. If the sequence is wrong, swap two of the incoming lines to correct the rotation direction.
- Ground the motor: Always ground the motor using the designated grounding terminal. This will prevent any electrical accidents.
- Test the connections: Before turning the motor on, double-check all connections, ensuring that everything is tight and secure.
Once everything is checked, turn the power back on and test the motor. The motor should start running smoothly, and you should observe no unusual sounds or overheating. If there are any issues, it’s important to switch off the power immediately and recheck the connections.
Troubleshooting Common Three-Phase Motor Wiring Issues
Overheating Due to Phase Imbalance
One of the most common issues with three-phase motors is overheating caused by phase imbalance. This occurs when the three phases aren’t providing equal power to the motor, which can cause one phase to carry more load than the others. As a result, the motor windings on the affected phase can overheat, leading to insulation failure and eventual motor damage.
How to Fix It:
- Check the current in each phase: Use a clamp meter to measure the current on each of the three phases. If you notice significant differences, there’s a phase imbalance.
- Correct the imbalance: You can fix phase imbalance by balancing the load across the phases or, if needed, by adjusting the power supply. In some cases, a transformer or a phase balancing unit may be necessary to correct the imbalance.
Incorrect Motor Rotation Direction
Sometimes, a three-phase motor might rotate in the wrong direction, which can lead to damage or malfunction in the connected equipment. This typically happens when the phase sequence is incorrect.
How to Fix It:
- Verify the phase sequence: Before turning on the motor, use a phase rotation meter to check if the sequence is correct. If the motor is rotating in the wrong direction, simply swap any two of the three incoming power lines to correct the sequence.
- Double-check connections: Ensure that all wiring is correctly matched to the motor’s terminal markings. Also, ensure the grounding and neutral connections are secure.
Motor Not Starting
Another common problem is when the motor doesn’t start or operates intermittently. This could be caused by various factors, including a faulty power supply, incorrect voltage, or a short circuit in the motor windings.
How to Fix It:
- Check the power supply: Ensure that the power supply is delivering the correct voltage and that all breakers and fuses are intact. Use a multimeter to measure the voltage at the motor’s terminal box.
- Inspect the motor windings: If the windings are shorted or damaged, the motor will not start. A winding resistance test can help diagnose this issue.
- Ensure proper grounding: Without proper grounding, the motor may fail to start or could malfunction. Double-check the grounding and neutral connections.
Excessive Vibration or Noise
Excessive vibrations or unusual noise from the motor are often signs of mechanical or electrical issues. Possible causes include loose mounting, misalignment of the motor shaft, or problems with the bearings.
How to Fix It:
- Check motor mounting: Ensure that the motor is securely mounted to prevent movement during operation. Loose bolts or improper alignment can cause vibration.
- Examine the shaft and bearings: Check if the motor shaft is aligned properly. Misalignment can cause the motor to vibrate, leading to premature wear on the bearings and other components.
- Lubricate the bearings: If the bearings are dry or damaged, they can cause noise and excessive vibration. Lubricate the bearings or replace them if necessary.
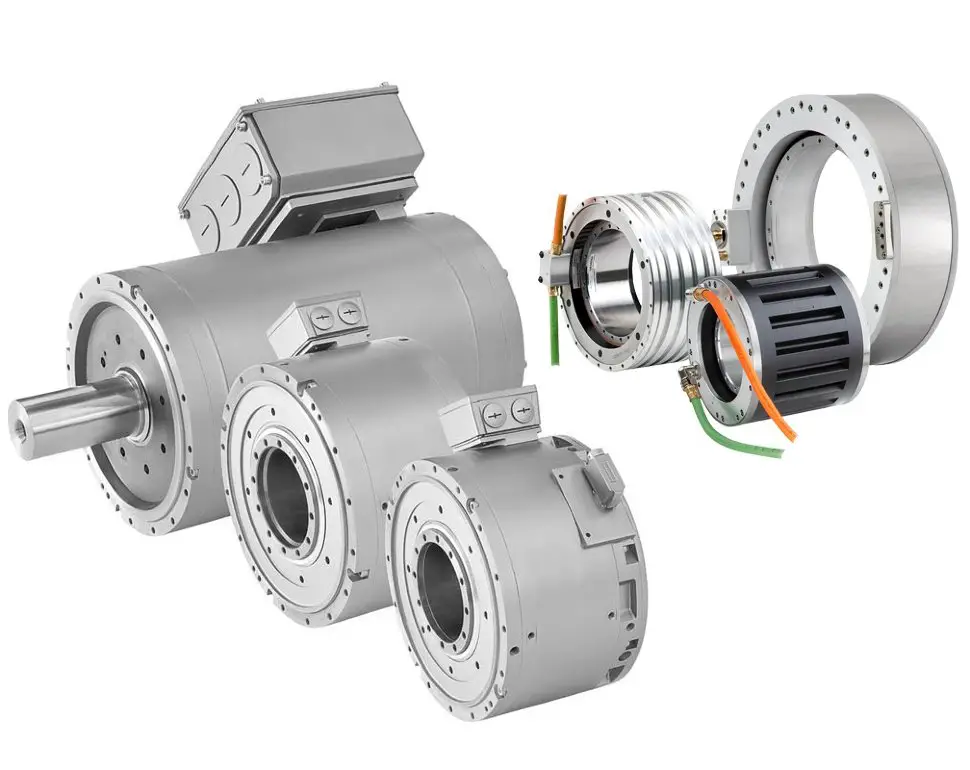
Overloading the Motor
Running a three-phase motor under conditions where it is overloaded can cause it to overheat and even fail. Overloading can happen when the motor is forced to run for extended periods at higher-than-rated load levels.
How to Fix It:
- Monitor motor load: Check if the motor is operating within its rated load capacity. Overloading the motor can lead to overheating and early failure.
- Adjust the load: Reduce the load on the motor by adjusting the connected equipment, or replace the motor with one that has a higher load rating.
Faulty Capacitors (in Synchronous Motors)
For synchronous motors, capacitors are sometimes used to start the motor or improve power factor. If these capacitors fail, the motor may not start or may experience erratic operation.
How to Fix It:
- Test the capacitors: Use a capacitance meter to test the motor’s capacitors. If they are faulty, replace them with new ones of the same rating.
- Check the wiring to the capacitors: Ensure the wiring to the capacitors is secure and that there are no shorts or loose connections.
FAQs
What is the difference between a three-phase motor and a single-phase motor?
A three-phase motor differs from a single-phase motor primarily in the way they receive power. A three-phase motor operates on three alternating currents that are 120 degrees out of phase with each other, providing a continuous, balanced flow of power. This results in higher efficiency, smoother operation, and greater torque. In contrast, a single-phase motor only uses one alternating current, which can cause fluctuations in power and lead to less efficient operation, especially at higher loads.
The added phases in a three-phase motor also allow for smoother startup and a reduction in the size of the motor required to perform the same tasks as a single-phase motor.
How can I check the phase sequence of my three-phase motor?
To check the phase sequence of your motor, you can use a phase rotation meter. This handy tool allows you to determine the order in which the phases reach their peak voltage. If the sequence is incorrect, you can reverse the phase connections by swapping two of the three incoming wires.
Ensuring the correct phase sequence is essential in applications where motor direction is critical. If the phase sequence is reversed, the motor may spin in the wrong direction, causing operational failures. This can lead to issues such as improper functioning of equipment, damage to machinery, or safety hazards. Correct phase sequence is especially important in applications like pumps, conveyors, and fans, where precise motor rotation is necessary for proper operation.
Can a three-phase motor operate on a single-phase supply?
While it’s not ideal, it is possible to run a three-phase motor on a single-phase supply using a phase converter. A phase converter essentially generates two additional phases from a single-phase power source, allowing a three-phase motor to operate.
However, this setup may result in reduced motor efficiency, lower starting torque, and increased wear. It’s typically recommended to use a three-phase supply for optimal performance.
What are the advantages of using a star (wye) connection over a delta connection?
The star (wye) configuration offers several benefits:
- It reduces the voltage on each winding, which lowers the current draw during motor startup, making it more energy-efficient.
- It’s ideal for dual-voltage motors, as it can handle both low-voltage and high-voltage systems.
- Star connections are often used when the motor needs to operate at reduced speed or lower torque at startup before switching to a delta configuration for full load operation.
In contrast, the delta connection provides higher torque and full-load capacity from the start but consumes more power, making it better suited for applications where maximum performance is required.
Conclusion
In this article, we’ve covered the essential concepts of three-phase motors and their wiring. We’ve helped you understand how to set up, troubleshoot, and maintain these powerful machines. We started with the basics of three-phase power and moved on to specific wiring configurations like star and delta. You’ve learned how these connections affect motor performance, efficiency, and longevity.
Whether you’re working with motors for industrial applications, HVAC systems, or heavy machinery, proper wiring is crucial. It ensures optimal motor operation and safety. By following the correct wiring steps, checking for phase imbalances, and addressing common issues, you’ll confidently manage your motor system. This approach helps prevent problems and maximizes motor efficiency.
Remember that regular maintenance, careful wiring checks, and timely troubleshooting can prevent most motor failures and extend the life of your equipment. As you gain more experience, you’ll be able to fine-tune your setup for maximum efficiency and reliability.
If you’re looking to dive deeper into three-phase motor connections or need resources for advanced troubleshooting and maintenance, be sure to check out the links provided throughout the article. With this knowledge, you’ll be well on your way to mastering the ins and outs of three-phase motor systems.